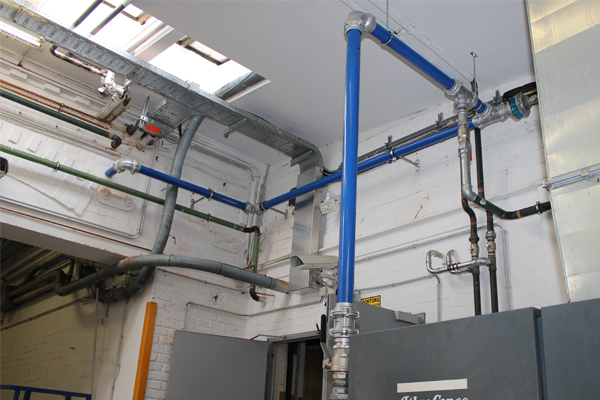
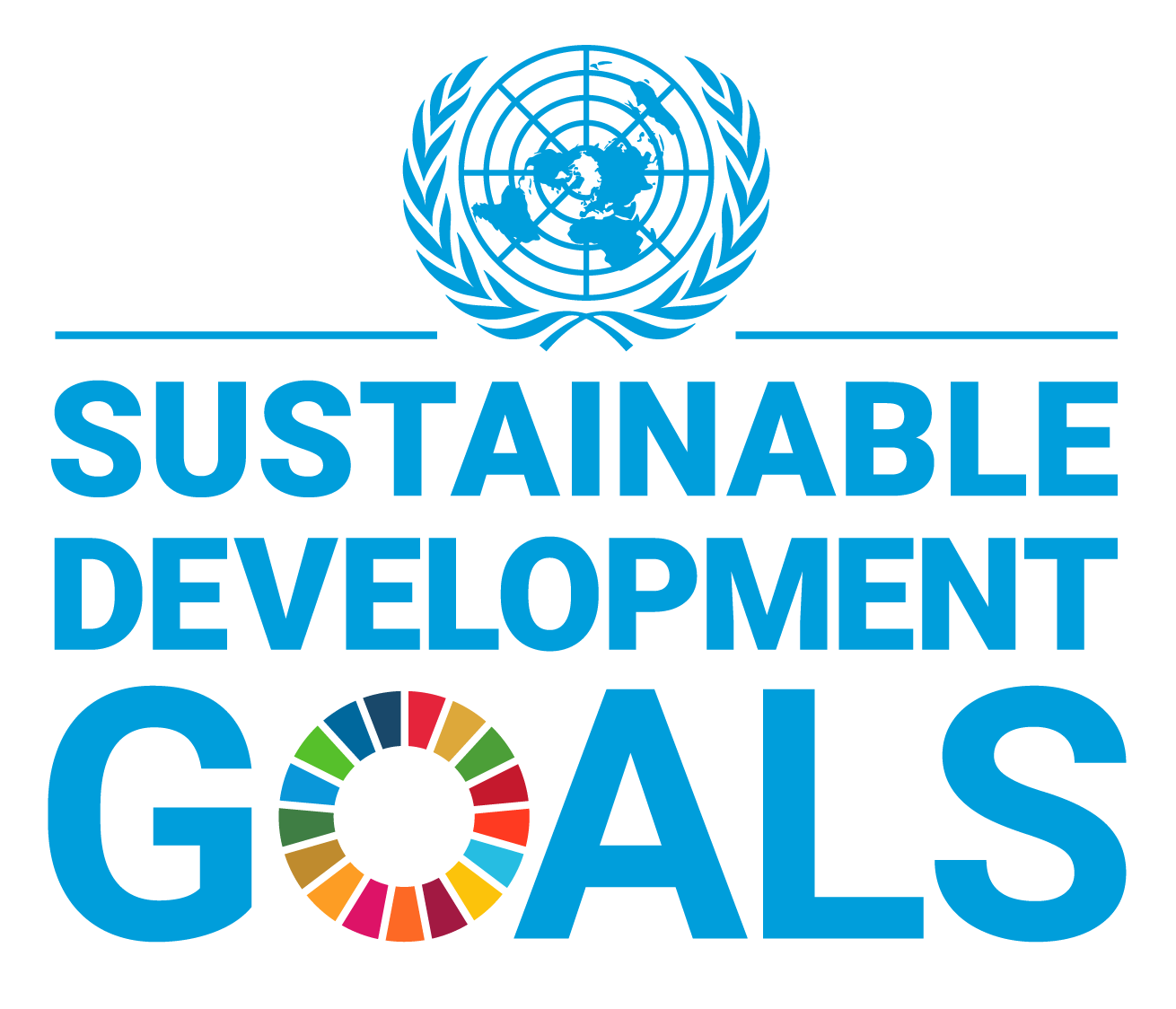
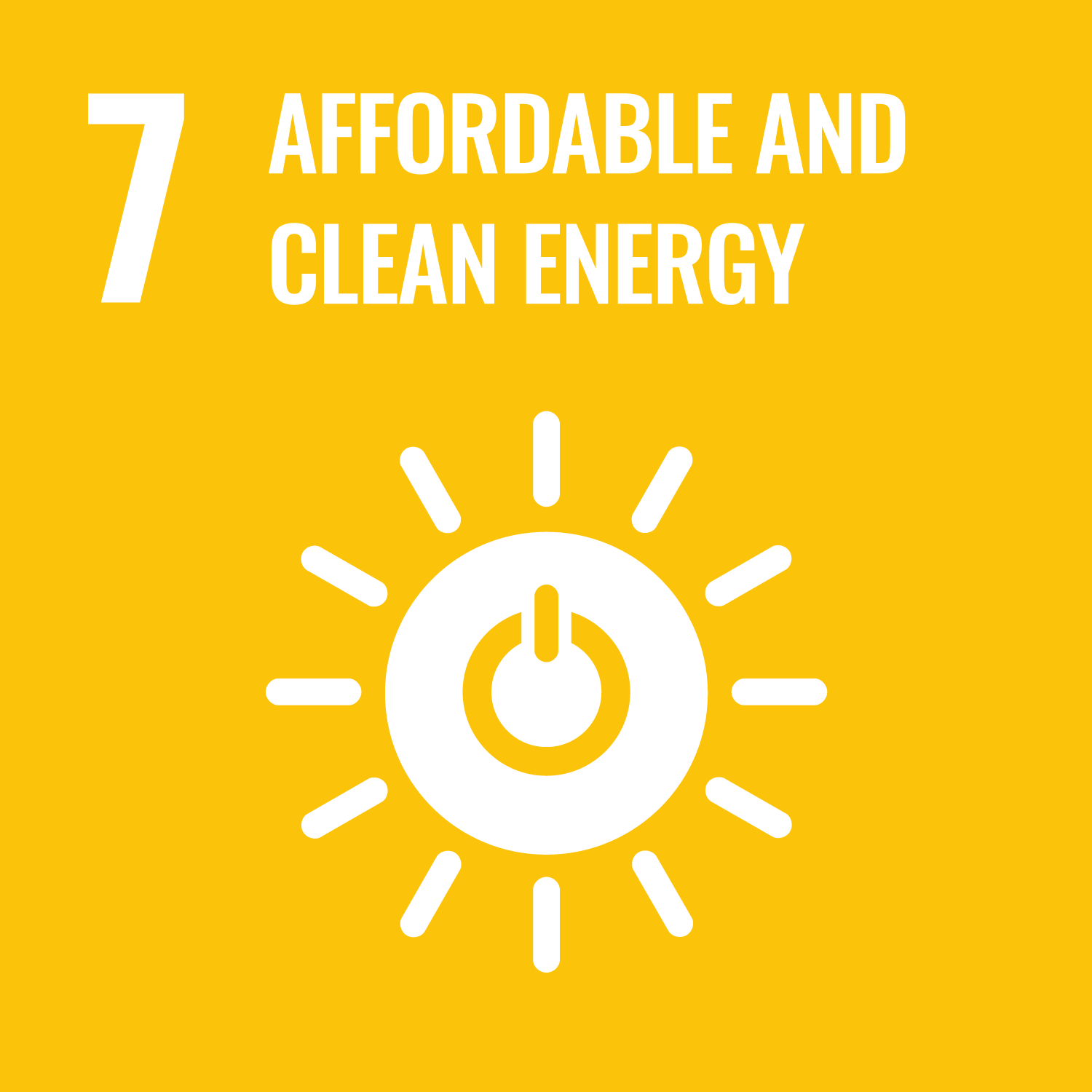
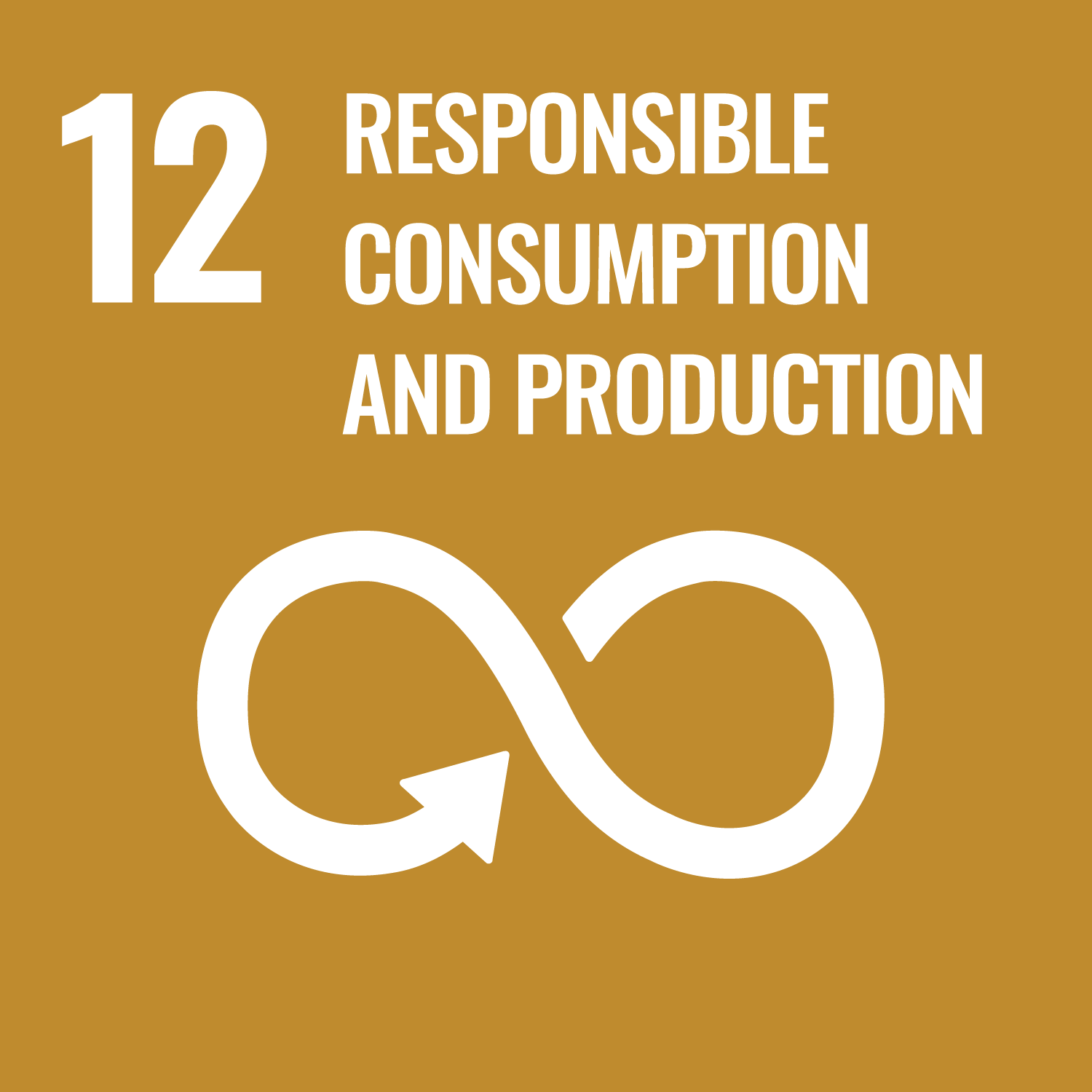
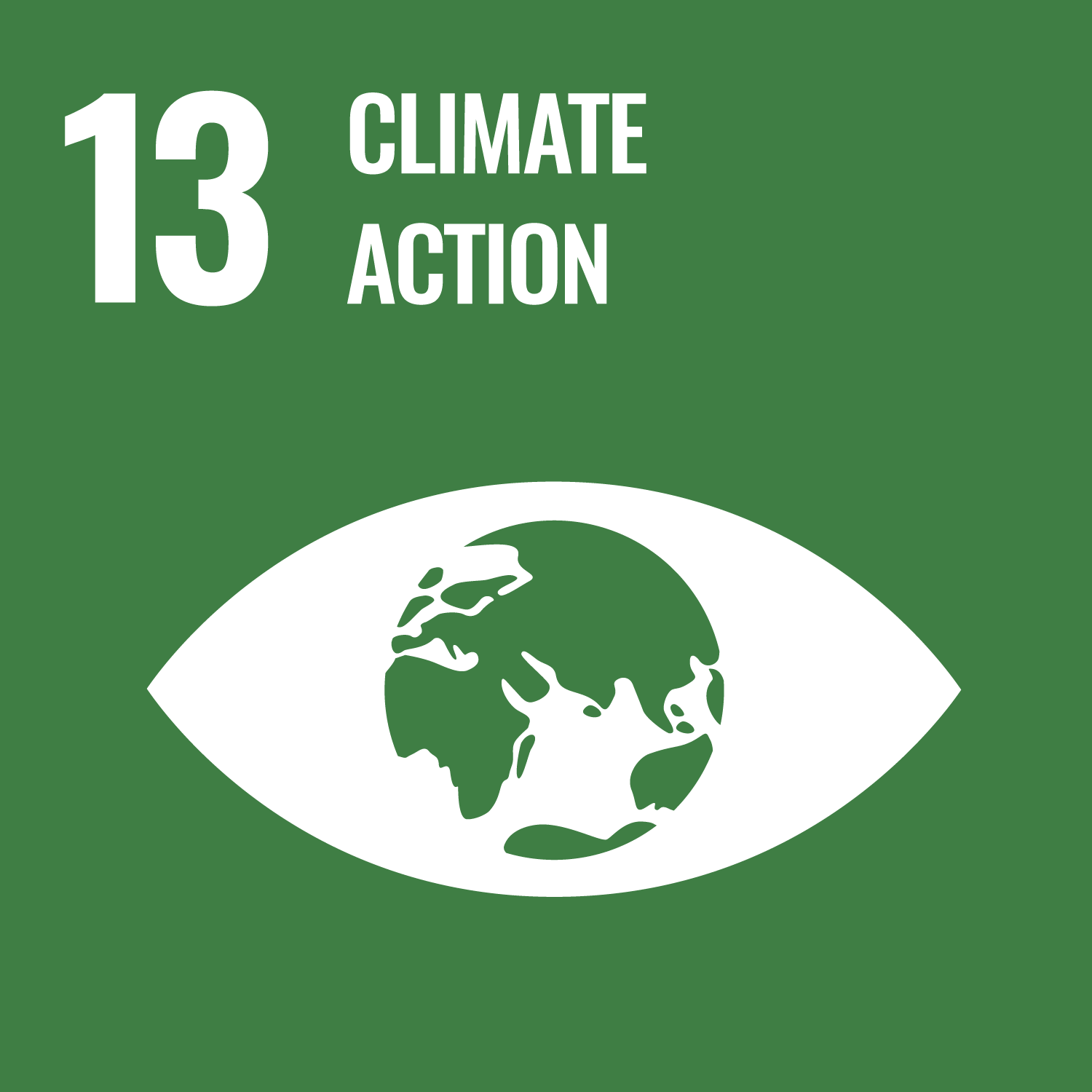
Behind the name "compressed air system optimisation" lies a small technical revolution at EVVA. In the past, three main compressors in three independent networks were still in use at the headquarters. They supply the compressed air for many manufacturing processes, e.g. for transporting parts within the machine or to remove the metal chips from the workpiece. Disadvantage: If a compressor failed, there was a problem delivering compressed air to the respective area. In addition, the compressors were unevenly loaded because they each had a different number of consumers.
The solution: A superordinated ring main system was used. The ring system now digitally controls and connects 4 compressors. They are now evenly loaded. This "Industry 4.0" project provides intelligent air pressure control and reduces maintenance costs. EVVA will continually increase the performance of the compressed air network in order to further strengthen reliability.
Very high energy savings ahead
Compressed air production is one of the largest electricity consumers at EVVA. EVVA currently requires around a fifth of its total electricity requirements per year to generate compressed air. It is therefore a main approach in the company to save more energy and CO₂ in the future, for example through:
- new, more energy efficient compressors
The more efficient the compressors, the lower the electricity requirement. EVVA has therefore already invested in two new compressors in 2022 - these are 15% more energy efficient than the old devices.
There are currently 4 compressors in use at the headquarters, which are necessary for the production of security cylinders, keys, etc. Two additional compressors followed in 2024. They are equipped with a smart control (optimizer) that prevents idle times and therefore wasted energy
Positive effects: This results in operational savings of 371,000 kWh per year or around 63,000 euros. The investment is amortised in 2.5 years. Another big advantage: EVVA can use the waste heat from the compressors to gradually replace the gas previously required for heating (more on this in the corresponding point under “energy management”)
-
Check compressed air lines
With new pipework and the installation of new valves and stopcocks, EVVA has eliminated leaks in the compressed air lines. This enabled the compressors to run for shorter periods and EVVA to save 74,000 kWh of energy per year (= electricity consumption of over 20 private households). EVVA is implementing further measures for the coming years
How would you like to share?